講座内容
構造、寸法を決める/コントロールソフトを決める/使用材料を決める/ノズルとホットエンド/冷却構造/部品を設計する/部品表を作る/部品発注
3Dプリンタを実際に作りながら考えるという刺激的なイベント「横濱3Dプリンタ実践ゼミ(全6回)」。今回からさらに内容が充実してくる。
3週間ぶりの開催だが、その間はまリンク取材班は自主学習のために「3Dプリンタではじめるデジタルモノづくり(門田和雄著)」を購入。この本は3Dプリンタの自作についての説明が充実しており、講師の増田恒夫さん(SHC設計代表)も執筆に協力している。少し前知識を頭に入れてからゼミに参加するのであった。
デルタ型3Dプリンタを丸裸にする!
前回は3Dプリンタを動かすために必要な役割の異なる数種のソフトウェアについて学習した。まず、3Dデータを作成する「3D-CAD」。次に、3Dデータを積層造形が可能なデータに変換し、3Dプリンタの制御コードであるG-Codeに変換する「スライサー」。そしてスライサーの操作やプリンタへのデータ送信などをおこなう「フロントエンド」。プリンタ本体に組み込まれ、G-Codeを解釈してモーターやヒーターをコントロールする「ファームウェア」だ。
このゼミでは、プロの技術者を対象とし、デスクトップで使用できる熱溶解積層方式(FDM)の中型デルタプリンタを開発します。3回目は「3Dプリンタを設計する」ということですので、仕様書と部品表をお渡しします。
今回はデルタ型3Dプリンタを構成する部品一つ一つを丸裸にするプログラムだ。増田さんから、製品仕様書に加え、開発者用にさらに詳しく記載された機能仕様書が配布された。鎮座するむき出しのロボットを前に増田さんは続けた。
私はパラレルリンク技術を用いた製品開発のネットワークをこの横浜で立ち上げたい。名づけて『横浜デルタネットワーク』。どうですか?(笑) 私はデルタ機構を用いた技術者同士のゆるやかなつながりを作って、皆さんたちと一緒にこいつの改良アイデアを出し合いたい。だから、こいつはその実験機です。
デルタ型3Dプリンタの解剖図を読み解く
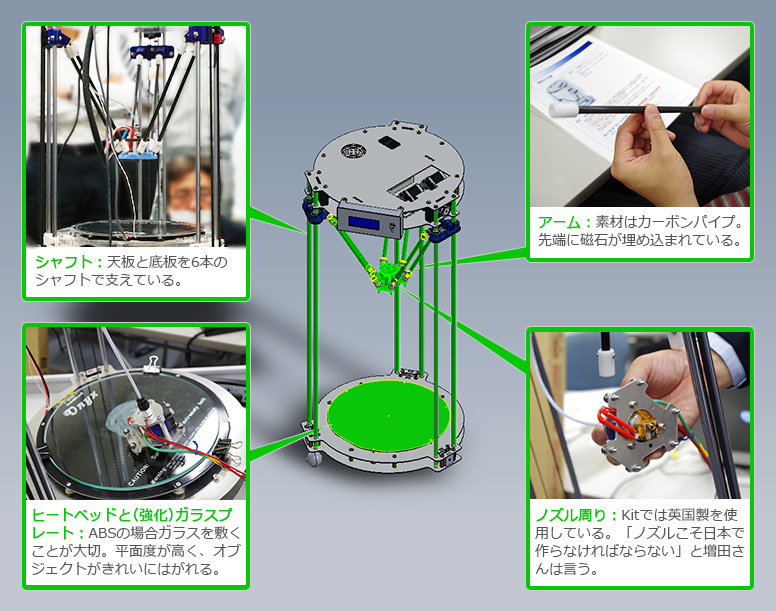
概要は、アルミの板金でできた天板部と底板部。この天板部と底板部をリニアシャフト6本(3か所)で支える構造だ。それでは、今回製作するデルタ型3Dプリンタの機能仕様書をご覧いただきたい。
機能仕様書
機能仕様書とは、製品仕様書を基に開発部門がより詳しい機能を記載するもの。実際には要求規格や試験方法、その判断基準が記載される。なお、現時点では3Dプリンタに安全性規格はない。
項目 | 内容 |
---|---|
造形方式: | 熱溶解積層方式 |
外形寸法: | 直径420mm 高さ830mm以下 |
造形サイズ: | 直径250mm 高さ370mm |
重量: | 15kg以下 |
使用材料: | PLA、ABS |
使用環境: | 10°C~40°C 湿度90%以下の室内 |
プレート材料: | 5mm強化ガラス |
ノズル径: | 0.4mm |
ジョイント構造: | ネオジムマグネットジョイント方式 |
ホットエンド: | E3D社 all metal HotEnd採用し、高温溶融材料に対応 |
エクストルーダ: | SeeMeeCNC社のEZStruder Cold End Kit採用(ダイレクトドライブ方式) |
使用ソフト | フロンドエンド: Repetier-Host ファームウェア: Repetier スライサー: KISSlicer |
現状の課題は「熱」「構造」「ノズルまわり」かな?
製品として完成しているように見えるが、増田さんは、未解決課題がたくさんあるという。
増田さんが指摘する諸問題を素人ながらに3つのポイントに絞ってみた。
<熱・温度>の問題ガラスプレートを温めるために設置するヒートベッドの熱を効率的にガラスプレートへ伝えられない。
室温が低すぎるとヒートベッドが温まらない。ヒューズが飛んでしまうことがある。
<構造>の問題ピボットとアームの構造。素材に改良の余地が残る。(現状は)低コストでの製造が難しい。
全体を支える支柱の強度に改良の余地が残る。(現状は)ねじれが生じる可能性がある。
造形には厳密なキャリブレーションが必要。(現状は)アームは手動で設定しており非効率である。
<ノズルまわり>の問題ノズルの詰まり対策。フィラメントのテンション機構の必要性がある。
フィラメント押出し部、エクストルーダに改良の余地が残る。
熱・温度の話
ABSを使って横方向に長いオブジェクトを作ると端が5mmくらい反ってしまうんです。そのためにプレートを温めないといけない。温めるために敷く皿を「ヒートベッド」といって、100°Cくらいまで温まります。今回はオプションで付けますが、PLAの場合は温める必要はないです。あと、直接ヒートベッドに出力するとヒートベッド自体が膨張してオブジェクトに影響します。だからABSの場合はガラスを敷くことが大切です。
ガラスは強化ガラスです。ガラスは光沢があって平面度が高い、きれいにオブジェクトがはがれるから好都合です。しかも安い。通販で3,000円くらいです。大きさと厚さを指定すると届きます。本来は耐熱ガラスを使いたいですね。私が強化ガラスを使うのは温度を上げるつもりがないからです。金属板は粗いし、熱で変形するので避けています。将来的にはガラスに熱線が付いているヒートガラスを使いたいですね。
材料としてはPLAの方が自然素材だし何かとよさそうだが、素材に粘りがないのでヤスリがけが難しいらしい。耐熱ガラスは熱に強いが強度が弱い。強化ガラスは強度はあるが熱に強くない。どれも帯に短し襷に長し…な状況のようだ。
使用環境も重要です。先日、テクニカルショウヨコハマのIDECブースに出展したんですが、搬入日(2014年2月4日)はとくに寒かった。パシフィコ横浜の搬入扉は開けっ放しで吹きさらし。だから全然ヒートベッドが温まらず、ヒューズが切れてしまった。室温10°C以下はきついですね。
はまリンクも2月4日はパシフィコ横浜で出展準備中でした! 確かにむちゃくちゃ寒かった。屋外で3Dプリンタのイベントをすることがあったら気をつけないといけませんね。
構造の話
ヘッドと軸(アーム)は簡単に取り替えられるように磁石でくっついています。これ、アメリカの開発者のアイデアなんです。ネットの掲示板にありました(笑)。磁石を使うからピボット部分は鉄なんです。だからフィラメントが溶ける際に出るガスによって錆びちゃう。よくないですね。
アームの素材はカーボンパイプです。コンマ1mmレベルまでヤスリで研いでくれるところがないから開発の支障となっている部分の一つです。あと、カーボンは接着できない。だからネジ止めをしてます。全体的にネジが多いです(笑)
磁石にヤスリ、ネジ止め…ずいぶんと身近な部品でできているんだ。
シャフトが長いのは短くても値段が変わらないからです(笑)。ただしシャフトが長いと全体の剛性が落ちてしまう。上下のアルミ板だけで強度を保っているので、ねじれが生じてしまう。補強して剛性を加える工夫が必要ですね。アルミのフレームなどで強度を上げることを考えています。ただしジョイント部は重い方が安定するという面もあります。
はまリンクとしてはこのデルタ型3Dプリンタの外装デザインのアイデアコンペを企画したいな。
Carriage Horizontal Offset: | 38.4mm |
Printer Radius: | 200mm |
Delta Radius: | 128.6mm |
Delta Diagonal Rod: | 286.6mm |
End Effector Horizontal Offset: | 33mm |
デルタはとにかく動きが美しい。X.Y.Zの三軸構成だから動くのがノズル部分だけです。X.Yの二軸のものはZ方向に動く時にプレートが動くものがある。デルタはプレートが動かない。これが一番の違いです。ただし正確かつ安定して出力させるためにおこなうキャリブレーションの課題はある。今は補正値を入力する方法と手動の二つのやり方があります。私は手動なんです。本当は自動でできるセンサーを入れたいんです。きっちりキャリブレーションをするときれいに仕上がります。そうするとこいつがさらに愛おしくなる(笑)
デルタはアームの動きがバレエダンサーのようにしなやかなんだ。二軸ものは、ブレイクダンスというかロックダンスなんだよね。
ノズルまわりの話
ノズルは本当に困っています。今は英国製を買っています。なんでか? 日本で作ってくれないからです。加工コストが高く、しかも少量では作ってもらえない。ノズルこそ日本が作らないといけないものなんです。
ノズル径は0.5mmだとかなり粗い造形になる。0.3~0.4mmくらいがベター。ただし細いと積層に時間がかかるし、斜めに動く時にラップする範囲が減る。細ければいいわけではない。中国製の中にはノズル径0.2mmなんてものもあります。これはフィラメントが詰まった時に大変です。詰まると、力技で固まったフィラメントを取らないといけないのが現実です(笑)
ノズル径の問題は、造形の美しさを取るか、使いやすさをとるかのせめぎ合いのようだ。
ノズル部断面図フィラメントを押し出す「エクストルーダ」とフィラメントを溶かす「ホットエンド」が近接しているものもありますが、ノズル部分は極力軽くしたいので、こいつの場合は上の天板に設置して、ホットエンドと離しています。エクストルーダが温まると、フィラメントが柔らかくなって押し出せないので離すのは好都合です。
ホットエンドの熱が他の部品に伝わらないように冷却用にファンを取り付けます。さらに、出力したフィラメントはすぐに冷やさないとうまく積層していかない。だからノズルの先端部は冷やさないといけない。そのためにヒーターのあるホットエンド部分とノズル部分を切り離し、アルミ板ではさみ込んだ二層構造とし、熱が伝わらないようにしています。
頭を冷やして、腰から下を温めるけど、足の指先は冷やす…だらしない半身浴みたいな話だ。
ノズルから出力したフィラメントは、冷えて固まっていないと次のフィラメントが乗っかっていかない。ですから小さいものを作る時は熱いまま、きれいなものができない。でもね、余計な話ですが、フィラメントなんかやめたいんです。だってペレット状のものを糸状に成形して、それをまた溶かして造形するって…。ばからしい面もあります。だから材料のプロジェクトが必要なんです。
最後は材料の根本的な話になってしまった増田さん。熱溶解積層方式(FDM)の3Dプリンタはフィラメントありきではないことを指摘した。確かにペレット状の樹脂をザーッと窯に入れて、きちんと樹脂が溶けてノズルから出てくれば問題のない話だ。蒸気機関車タイプの3Dプリンタもありかもしれない。
部品は全部で62種類! 次回から組み立てるぞー
増田さんは、冒頭に「未解決課題がたくさんある」と言っていたが、一つ一つ説明を聞ていくと「なるほど…」と納得してしまう。デルタ型3Dプリンタにはまだまだ改良の余地があるようだ。自作したロボットの詳細な仕様書まで惜しげもなく公開してしまう増田さん。その根底には、欲しい人が欲しいものを作り、改良していったものが製品となっていくという人間中心設計の哲学がある。
増田さん自身も全開むき出しだ。
こいつの改良が容易にできるネットワークを作るために、今回は機能仕様書も使用部品も全部お伝えします。部品は62種類(注: 2/18時点)。そのうち3Dプリンタで作る部品は10種類です。
テキストの最終ページは詳細な部品表だった。そこに示された62種の部品たち。しかも3Dプリンタで3Dプリンタの部品を作るとは!
実際に組み立てたモデルはお安く提供します。今回のゼミは、申込者が多くて、全部で8台作ります。残り2回で組み立て、最終回に出力します。私の1台も含めて、デルタ型3Dプリンタが9台並ぶのはたぶん世界初ですよ(笑)
じゃあ、最終日は「横浜デルタネットワーク」旗揚げ公演、演目は「デルタ型3Dプリンタ版白鳥の湖」ですね!